High Pressure Gas Lift with Xstream Lift
0:00 This podcast is brought to you by EnergyX. Are you tired of paying huge rates to the big cloud providers? Are you worried about being booted off a cloud platform? If your company doesn't meet their
0:10 ever shifting standards, ready to step up your data security and disaster recovery game? Well, ladies and gentlemen, your new cloud is ready. Introducing XCloud, the scalable, resilient,
0:19 computing cloud that is also actually affordable. It's high performance compute for half the cost. HPC for HTC XCloud from Red Team is opening a beta program for new cloud computing customers, and
0:32 that means you, my friend. This cloud is powered by the XMDC, immersion-cooled modular data center from EnergyX. I've seen the data center in operation and it is its total game changers. If you
0:42 want more information about the beta launch, go to the URL in the description. Type in promo code betaBETA for 50 off of your first instance. And so the URL is going to be
0:54 digitalwalkcutterscomenergyx Brandon, tell me real quick, you know, what is.
0:60 extreme of. It's actually pretty cool, man. I was there, you know, when in the early days, when you're talking about doing it and been a little bit quiet about building it. And so now you're
1:10 coming on the show and talking about it. So one, I appreciate you coming here and taking the time, but tell me what you're working on. Yeah, thanks. Thanks for having me, Colin. So extreme
1:21 lift is kind of bridges the gap between artificial lift and compression And so what we do, and I'll get into the specifics a little bit later, but what we do is we build these high pressure gas lift
1:34 units that are used for gas lift. Don't need any valves down hole. And this technology, it helps, it helps you get more production than any other artificial lift method on the market. And it's
1:50 like the simplest thing that you could even think of. You brought me these stickers. This is 4000 psi straight up your annulus Yes.
2:01 this is a good sticker. We need to talk about that a little bit. We're going to dive into this because I'm not a production guy. We're going to strip it down to some of the basics of artificial
2:11 lift. But tell me a little bit about your background.
2:17 You've been working in artificial lift and production all of your career. Am I right on that? So I grew up in Calgary,
2:26 got a degree in mechanical engineering in the US, and then went back and forth. It was kind of during the 2008 financial crisis that I was going to school. But the oil and gas business in Canada
2:40 was doing really well at
2:48 the
2:52 time. So I was working in Canada going to school in the US, kind of going back and forth, interned with Canadian natural resources up in Fort McMurray in the oil sands. I did an eight month co-op
2:56 term with them. And then when I was graduating, I interviewed with a lot of different companies.
3:02 And one of them was EOG, and I interviewed with them in the US and they were always looking for Canadians to send up to their Canadian division. And when I talked to the Canadian guys, they
3:16 basically had this little field in
3:21 Wascada, Manitoba, which is like
3:23 15 minutes away from the US border in North Dakota, 140 people in this town, and no one wanted to move there. So they found me and asked me if I wanted to move there, and I kind of snuck in the
3:34 Bactore-D-O-G kind of non-traditionally. Yeah. I didn't go through like the big, you know, internship, like two internships and all that stuff. They just, I said I'd moved to this little town
3:48 no one else wanted to move to and I moved there, so. They needed a warm body in this small town and you're willing to do it. Exactly It was a field of like 700 rod pump wells
4:00 You know, I spent a little bit of time in the office in Calgary, and then they moved me out to this little town in the middle of nowhere. I actually had to go across the border into North Dakota to
4:10 go to Walmart. Oh, really? Yeah, I had to go through the border crossing to go get my groceries every week, and I even had a PO box in North Dakota to get Amazon packages. So I could get them to
4:21 my house in this little town in North Dakota. Did you have to go to bot? No, OK
4:29 Yeah, that's, I mean, I've been to North Dakota several times. And, you know, up there, you can get in the middle of nowhere, you know, pretty, pretty quick. And having lived up in those
4:41 remote places. And even now I live in Midland now, but you, you spend time in these places. You're like, how did people homestead these places? Yeah, no, I have no idea how people survive.
4:50 That was my biggest takeaway when I spent a month on the North slope of Alaska. It's like, how did the Inuits live up here as like it doesn't make any fucking sense to me. humans were able to do
4:60 that and yeah, I don't think most of society, I think it's something that we're privileged to working in oil and gas that you
5:09 truly get to be out in the middle of nowhere and gives you kind of perspective. It's always in the extremes, like either like negative 40 or colder or like 110 or hotter. What I've learned is that
5:21 we never drill for oil in nice places, you know, it's always extremely harsh, but even, you know, in Texas, man, you know, I'd spend time out in the Guilford and, you know, I'm two hours
5:30 away from pavement on the Mexican border. I mean, even in just our home state, I'm like, dude, get out in the middle of fucking nowhere, you know, parts of West Texas. And so anywhere between
5:42 Pecas and Carlsbad, man, I mean, yeah,
5:47 so, you know, that's, that's that you can kind of paint it in that extreme. It's like how to drive to a whole 'nother country and go through border crossing to even get crocheted. Exactly. And
5:58 so, started my career up there, field-based production engineer, they handed me three workover rigs and said, Here you go, I had no idea what I was doing. The company men would call me and be
6:08 like, Hey, Wells on a VAC, this is what's happening in all this. It was just little rod jobs, but 3, 000 foot deep, 3, 000 foot lateral, so 6, 000 kind of TD Wells
6:22 And I just learned by doing, I mean, that's how I learned. I wasn't fantastic at school. I spent all my time in college in the math tutoring lab,
6:32 but I got through it. And so I just learned to roll our hands on. And I've been fortunate that I've always been kind of field-based in my positions and been able to touch things and see things and
6:43 be on the rig and all that stuff. So that's how I learned the best. That's an interesting point because, you know, the time that you came in the industry, you know, it's kind of a rise of shell
6:56 and horizontal and get a lot of engineers that, I mean, companies like Pioneer and UOG were catering to engineering students coming out of school, right? And kind of bypass that field experience,
7:11 which is kind of like an old school thing of like, you're an engineer, you go out to the field, but I'm just a big believer that that hands-on seeing it, like, you know, sorry for all the
7:21 engineers out there, but, you know, what you learned in school, it's completely different than what happens out in the field and actually seeing it. There's no parallel for real-world seeing and
7:32 touching things. Yeah, so it sounds like, you know, you're fortunate in that aspect and, you know, I love that you ate glass per eat shit, whatever you want to say, whatever you're eating.
7:47 but to go up there when no one else wants to, I mean, that's where the opportunity's at, right? It is doing the stuff that no one else wants to. So, EOG then moved me down to North Dakota. It
7:56 was moving south for me. There was a lot of, you know, how a lot of these
8:04 AM kids come out as college and the first thing they do is get married between when they graduate and when they start their jobs. Yeah A lot of
8:15 wives from Texas, from AM, weren't happy up in North Dakota. So they sent some Canadians down to North Dakota where we were a little bit more used to the weather. Yeah. Exactly. Yeah. Spent
8:29 about five years of the OG up in that area, doing a lot of really cool things. And I got really, again, that was field-based. I mean, I was in the Stanley office, right, in the middle of the
8:40 wells. I had a big group of wells that I was in charge of back then it was when.
8:47 the Bakken was absolutely blown and going. Yeah. Like it was before, it was busier than the Permian was at the time. Yeah. In like the early 2010s, right? Yeah. And so I got to see a lot of
9:01 action and a lot of stuff really quick.
9:05 We were using a lot of ESPs at the time. I got my hands on ESPs. I had some really good mentors at EOG and also just a lot of wells and a lot of activity. So I saw like the volume of stuff I saw
9:15 was so much so fast because in my area I was doing 60 new drills a year or something just in my one area, right? Yeah. And we had hundreds of ESPs in the field. And I kind of took interest in that,
9:30 took it upon myself to become good at that and become a technical expert for ESPs. And so that's kind of where this - actually, this high pressure gas of journey started because ESPs are like super,
9:43 super -
9:46 They're good at producing a lot of fluid and getting really good drawdown, but they're really complicated electromechanical machines and have thousands and thousands of moving parts. And you
9:58 basically plug in like, you set it 10, 000 feet deep and plug in a 10, 000 foot extension cord to surface, right? And there's these wells are so much that can go wrong It's harsh conditions,
10:10 right? Like you have your, your wellboard deviations from drilling these long reach laterals and trying to get your well spacing on from like a multi well pad and getting your well spacing down
10:23 whole. And you've got like, you're producing massive amount of sand and solids, yeah, and especially in the Bakken, like it's naturally fractured up there and those wells just seem to give up so
10:33 much sand for such a long time. Yeah And then your GORs are constantly going up and like, we're talking about remote, always drilling in remote places, like the electrical infrastructure isn't
10:43 good. the first word in electric submersible pumps is electric, right? So, like power quality isn't good, but everybody uses and still use ESPs because they're really good at moving a
10:59 ton of fluid really fast, right? Well, you know, that's something I'd actually didn't appreciate until last year. And, oh, actually, I think it was dumb that was talking about it, was talking
11:10 about quality of power And I didn't realize or appreciate how much production engineers within these EMPs understood or were paying attention to electricity quality coming from, you know, a
11:27 substation. And that's something that I don't think is like super appreciated. We're doing, especially with ESPs, dude. When I was in North Dakota, when we'd have like a bunch of ESPs go down
11:40 and we'd start them all back out, the town of partial would. have a voltage sag and people
11:47 had gen sets because we were pulling so much power in the old field from ESPs when you'd bring a bunch online at a time. That's insane. So let's take a pause here real quick and let's do some oil
12:01 and gas 101 for everyone out there. Obviously have a lot of production engineers here that know what an ESP is and how it functions and operates but have a lot of people from downstream, midstream
12:12 that don't. Can you just give us a high level overview of how an ESP actually works? Yeah. So an ESP is a centrifugal pump. Basically it's kind of like if you have a turbo in your car that little
12:27 impeller in your turbo that gives you your boost, that's a ESP stage basically. So what you do is you take those stages and you stack hundreds of them on top of each other So the different
12:40 components you have your pumps. Like starting from the top down
12:46 on your downhole stuff, right? You have all your pumps, which are made of ESP stages. And like I said, you have hundreds of them because each one of those stages produces so much head to lift
12:56 fluid. And if you're 10, 000 feet down, you need to add enough to get 10, 000 feet of lift to get lift to surface, right? And then
13:06 below that, you have like your intake and your gas separator, where fluid comes in, and of course, these wells produce oil and gas. So you have to have some sort of separation mechanism to try to
13:16 get as much gas out of there. Because if you get too much gas in an ESP, it's like when you're making a protein shake or making a smoothing or blender and you know, it sucks in a pocket of air and
13:27 then it spins real fast and it doesn't blend anything. That's essentially what gas lock is inside an ESP when you get too much gas in there where it'll it you won't be moving fluid through there and
13:39 that that pocket of gas will make it so bins, and it's not actually doing any work, right? And then you get to overheating and things like that and burning up motors. Yeah. And then underneath
13:50 your intake and your gas separators, you have your protector or your seal. And what that is, that's a barrier between where your fluid comes into the pump and then your electrical motor, because,
13:60 you know, electricity doesn't like being in water, right? So your downhole submerged in water, you have to separate and make sure, you know, your well bore fluid doesn't get into your motor and
14:13 contaminate your motor. So you have a protector or sometimes called a seal that has a bunch of chambers that filled with oil and that communicates with the motor oil to make it so that it's really
14:24 hard for well bore fluid to make it into the motor and short out the motor. And then you have a plug into your, to your ESP called a pothead and that plugs the cable in basically a however deep your
14:36 well is 6, 000 foot, 10, 000 foot extension cord to surface. And then on the bottom of the motor, you have a sensor that measures the temperature of your motor, the temperature of the fluid,
14:45 and the bottom hole pressure. To your point, I mean, you can tell this is a complicated piece of machinery, and it's ran down, you know, 10, 000 feet in the ground, 50 to 150, 175 foot long,
15:03 and each component is no longer than 20 or 30 feet, right? Yeah Or making lots of connections, like the
15:11 motor itself is, because electric motors increase with horsepower in
15:19 diameter, they increase in horsepower, like squared in diameter. But in a five and a half casing, well, five and a 20 pound casing, well, where you have 478 ID, like
15:35 465 drift I mean, you're talking about a 45 inch motor. And in order to get the horsepower you need, like you need 400 horsepower for some of the new wells. So you just gotta stack a bunch of them.
15:47 You have two 30 foot motors you're putting on top of each other, right? With all the electrical connections that have to go together just right on a rig floor in the middle of North Dakota and
15:57 negative 40, or in the middle West Texas, at 110 when a habobes coming in, right? And so like the rig floor is not the cleanest place in there, so you have like all these electrical connections
16:09 and you're making connections to mechanical and electrical connections, like five, six, seven, eight of these connections to stack up this string that's 150 feet long or sometimes 175 feet long.
16:21 Not even counting the bottom whole assembly or whatever sand protection you put on top of it. And then you're running in on tubing and spooling the cable and spooling chemical injection line while
16:33 you're running in and either banding it to the tubing or you're clamping it.
16:40 there are so many quality things, like so many things that can get damaged or nicked, that can reduce the reliability, run time with the ESP, that you really have to do everything really, really,
16:53 prudently and really write and fall procedures to get the best chance for it to run the longest and in the old field, that's not always the case, right? It's never the case. No. So that's
17:06 actually fascinating to me because I've never seen an ESP assembled and you know, spent a lot of my life on workover rigs and running tools, but I've never actually seen an ESP built and so having
17:17 you articulate this, I'm like, that sounds like a nightmare to be doing that. And even if everything goes right, you know, just downhole conditions are rough. And so, you know, to kind of
17:29 illustrate this for everyone, you know what you're talking about with the horsepower and idea of the casing issue, It's like your casing's down whole. You have whatever ID. you have, that's what
17:40 you have to work with. And you're talking about, you know, fitting something that's four and a half inch and a, you know, 475 ID. I mean, that's not a lot of space in that annulus to, and then
17:50 you're running cables and things of this nature. And so, you know, things getting nicked up. And so, yeah, that's just, I didn't realize that it was that delicate and intricate of a process to
18:02 assemble those and actually get them down whole and working. So that's, no, thanks for sharing that And so,
18:11 all right, so we'll side tangent from your story, but that was great. So I was at EOG. I was doing a lot of ESP stuff. I became one of the, you know, for the Denver Division, one of the ESP
18:21 guys there and
18:25 traveled around to a lot of the, you know, all over North America, all the ESP chops, doing, you know, quality stuff, tear downs, you know, audits, designs, all that stuff So, it.
18:41 So all the production engineers will appreciate this. When you're a production engineer, you're always getting pressure for management to produce more, right? We want more production, but you're
18:51 also getting pressure to spend less money. And usually those two things can generally, they go in the opposite direction. If you're trying to produce more, you're gonna spend more money. If you
19:02 wanna
19:04 spend less, you're gonna produce less So you're always trying to find like, especially with ESP reliability and how expensive they are, like these are hundreds of thousands of dollars, when you
19:17 buy one, plus your work over costs and all that stuff, so. So you're always playing this game of like, okay, we wanna change artificial lift types, so we'll go from ESP to gas lift, and then or
19:30 ESP to rod pump. And you're constantly trying to use these other artificial lift types to get a. lower cost profile than your ESP, but still match the production. And it's very hard to do unless
19:43 your well's down at 500 barrels a day already or under 1000 barrels a day. Yeah. And so we were trying to go to GasLift and conventional gas, so just couldn't get us there, right? So we're trying
19:56 to figure out
19:59 a way to get away from ESPs, but not sacrifice on the production. Yeah. Yeah. You wanted your cake and to eat it. Yeah, exactly. Go into GasLift a little bit and give us a rundown like you just
20:10 did on ESPs on
20:13 GasLift and why you guys are trying to go to that. Sounds like a cost basis. Yeah. So GasLift is generally on the capital side. You spend all your money on surface on like injection lines and
20:26 compression and everything, but on the OpEx side, it's extremely cheap. All you have is tubing in the hole, right? Just Just think about tubing. Sometimes you'll have a packer down hole.
20:34 Sometimes it'll be packerless and you'll put. a gas of valves in there. Basically, gas of valves are these little points of entry down the tubing string that are spaced out and they're pressurized
20:50 so that they open and close at a certain pressure. And then you get a compressor and you inject gas generally down the casing side, the annulus between the tubing and the casing, and down into one
21:03 of these valves And depending on how it was designed,
21:09 it's designed to get it like in the top valve. And as your bottom hole pressure decreases, then that top valve closes and forces a gas down to the next valve. And then your bottom hole pressure
21:20 decreases as you produce more barrels and then that valve closes and you work your way down, down your valve string, or down your tubing string on your valves.
21:30 And then all you really have is tubing that your production is going up So it doesn't matter if you're producing sand, doesn't matter if you're producing sand. Plug parts doesn't matter. The more
21:39 gas the well produces, the better, right? So you're not fighting gas like you are an ESP. Yep. And then if your well's deviated, it doesn't matter 'cause you don't have cable in the hole, you
21:47 don't have really have anything.
21:50 Much more of a mechanical system. Yeah, fewer points of value here, yeah. Actually, gas lift does really well in all these areas where all these tough things that unconventional wells throw at
22:02 you, right? Like everything that ESP is weak at, gas lift does great. But the problem with gas lift is, you can never get, especially on new wells, it's really hard to get the same production
22:15 as ESPs. And the, there's two reasons. The first reason is you're limited on your injection depth. So traditional compression is limited to roughly 1, 200 psi injection pressure, sometimes as
22:30 high as 1, 400, but the rule of thumb is generally 1, 200 psi. And it's my opinion, this is just me, like gas levels exist because compression falls, traditionally it's falling short. So on a
22:46 high bottom of a pressure well, you get a compressor, it outputs 1200 psi, and say you can only get, force your weight, a quarter of the way down the hole, right? Because the bottom of pressure
22:58 is too high to get all the way down. So that's where you put a gas level valve, and then you just work your way down from there So gas if works by lightening the fluid column, so you inject gas
23:09 into the tubing, and it reduces the density of the fluid in that tubing. So the pressure of the well can flow it on its own. And then as the bubbles rise and they expand, there's some lifting
23:21 effect there as well. But think about, you have like a 10, 000 foot deep well, and you're only lightening, reducing the density of like the top 2, 500 feet. That's what conventional gas lift
23:33 does. Conventionally, you're injecting down the casing and producing up the tubing, and that two and seven eighths tubing on the inside is only like 2441
23:44 ID. And so it's really small, like take a tape measure and measure out 24 inch radius or diameter, and there's not a lot of flow area there. And so what also happens is you bump up against
23:59 hydraulic friction where the friction and the tubing, once you get to a certain flow rate, is so high that you can't get above that flow rate. It's like terminal velocity falling down a plane with
24:09 wind resistance, right? Like you hit a certain velocity and due to wind resistance, you just stay at that velocity. With conventional gas lift up tubing, you hit like hydraulic friction
24:20 limitations and you can't produce more than that because the friction, the dominant force is friction. Yeah. And so you're limited by both injection depth and friction.
24:32 So with commisional gas lift system, you're essentially going and doing it in sections through these valves, you know, 2500 feet, 2500 feet, whatever that interval is. Yeah. So this
24:45 parlays into what you're doing with extreme lift, obviously. Just going to take a guess here. You saw this issue and said, hey, it sounds like to you, you're like, the actual problem is on the
24:57 compression side and not having enough force And then I'm also 4, 000 psi straight up your annually. So I'm like, I'm kind of striking. I think the dots and seeing where this is going.
25:10 What was your take on solving the issue? I can't take full credit for coming up with the idea. But what happened was when I was at EOG, they were really good at facilitating cooperation over the
25:23 entire company So we would get together like every year as
25:29 like production engineers from all the different and the different basins around the US and in Canada. And we would like have like a week long or three day workshop on some topic. And it was usually
25:41 some topic that one specific division was strong at, right? And we had in that division. So one year in the Denver division where we ran a lot of ESPs in the Bakken, we had a three day workshop on
25:54 ESPs. And we would have like a ESP training from some technical professional that trained us on ESP stuff And then we would present to each other and share what we were each doing in our respective
26:07 areas and kind of brainstorm and learn from each other and all those things. And so another one we had was rod pumps early in the Eagleford's life. They're running a lot of rod pumps. We had a rod
26:20 pump one in the Eagleford. And in 2015 around just before Christmas, 2015, we had one in Tyler, Texas and it was around Gaslift And so really that, that, That workshop meeting
26:36 was the genesis of high pressure gas lift today, where we all got together and we were presenting to each other the issues we were having with ESPs, like in the Denver division with gas lift. In
26:48 the Denver division, we were trying to go from ESP to gas lift and couldn't get the rates. Barnett was doing, had these older Barnett wells that were low pressure and they were able to not run any
27:00 valves and do poor boy gas, gas lift around the end of tubing. And then you had, you know, the Eagleford that was moving away from rod pumps and going to gas lift and was having, you know, gas
27:10 of valve failure issues and things. Then you had the Permian that was just starting to blow up and they were doing gapal and old wells and other things. So we're all talking to each other and
27:20 presenting to each other and brainstorming together. And basically what came out of that meeting was If we had compression with higher discharge pressure,
27:33 And, oh, and Tyler Texas had these new Buddha wells, that were pretty good wells, and they were doing annular gas lifts, so injecting down the tubing, producing up the casing. And so, we kind
27:47 of put all these things together as a group, and we're like, man, if we just had enough compression, like high enough discharge pressure, that we didn't have to use any gas lift valves, then we
27:57 would get rid of any issues with gas lift valves. Then if we could produce, go down the tubing, produce up the casing, then we'd get monster rates 'cause you'd get rid of that friction because in
28:08 the casing, that casing area between your tubing and casing is almost three times bigger than up your tubing. So you'd get rid of any friction limitations. And so through that brainstorming, all
28:19 these things came about. And so we each went back to our respective divisions and solicited compression companies to build compressors and almost nobody wanted to do it. Oh, really? Why do you
28:29 think that was?
28:33 Traditionally, compression likes to, they like to build units that won't sit in the yard if they don't have an application. So they build things that will work in a lot of different scenarios,
28:46 right? So something, the same machine they might be able to use for gas lift, going to multiple,
28:55 and sending gas multiple pads as in like a gas plant or for midstream, right? Like they don't want it in the yard eating grass Yeah, they want a general use compression system that they can utilize
29:04 across different assets. And in the industry, the downhill gas lift guys and the compression guys don't talk. Like there is no service company that does both, right? Like the downhill gas lift
29:20 guys just say, give me gas, give me compression, tell me what it's going to be, tell me the injection rate and the pressure and I'll design for that. And the compressor guys are like, just tell
29:29 me where to drop this unit off. And if it's not on skid, I don't care about it. All I care about is what's on my skid and that's what I deal with. The opportunity always sits at the intersection
29:40 of things. And I see this all the time in different businesses. And so it's a really interesting intersection right there's got these two parties and they don't talk to each other and don't
29:53 understand each side of it. I gotta go on a small tangent real quick. You mentioned EOG's Buddha Wells. Did you ever see our podcast episode? I look back and that wasn't for that. If you go
30:05 search EOG Buddha, like digital hotcatters comes up, it's a, now that you mentioned that, it's just further evidence that EOG's sitting on a huge Buddha pipe, but I have no insider knowledge. I
30:16 haven't worked for me for like, this is seven years. This is Braden's disclaimer. So with extreme, are you guys building the compressors? Tell me, you know, like what, what the actual,
30:30 product and services. Yeah, so we build this booster compressor. Okay. So it's just a
30:39 small gas of compressor, 3306NA engine, which is a pretty normal size for a single well gas lift, right?
30:50 But we engineer it in a way where we take the discharge pressure gas from your conventional compression at like 1, 000 pounds or 1, 200 pounds We can boost that up to over 4, 500 pounds. So you're
31:03 actually stacking this up with conventional compression systems. Okay, cool. Yeah, exactly. Cool. So for y'all, you know, from a business model perspective, you know, you go, I'm assuming
31:17 that you work with the EMPs directly in their engineering teams. Exactly, yeah. So to
31:24 back up a little bit, I left EOG
31:28 shortly after. like in 2017, I left DoG, we had done some high pressure gas up pilots with a couple companies that decided to, you know, try this out and build a few of them. And SM poached me
31:40 and brought me down to Midland, right? When they bought that Howard and Martin County stuff. And so when I was interviewing for that job, I had mentioned this high pressure gas of stuff that was
31:50 really, really nascent. And there's some interest from from my boss who ended up being my boss,
31:58 Nathan Loma over there. And so that's something that we we attacked and and wanted to do at SM as they developed this field, because we started with, I walked in there, they had 30 wells, 30
32:12 horizontal wells. By the time I left, it was over 330 wells, like three years later. But again, they started with ESPs and they initially reached out to me because I was, I knew ESPs and so I
32:25 came in, was an ESP guy, I helped. all their artificial lift strategy for that new area. And then we did pilot test with high pressure gas lift to compare against ESP in Wolf campaign and Wolf
32:39 can't be wells because those are the gas year wells out in the midland basin.
32:43 And then so I did that pilot and then I wrote an SPE paper about it
32:50 in 2018. And it was called like single point gas lift.
32:57 I forget what exactly what my own paper is called. So much you care about.
33:02 It's basically like a single point high pressure gas lift beats ESP in Permian basin pilot test or something like that. Yeah. Right. And so basically we had a pad with a bunch of ESPs on it and a
33:14 couple of high pressure gas of wells, high pressure gas of wells beat the ESP like huge. And then I was able at SM to roll this out like really, really large scale on a, you know, with our
33:26 development and do it on all the Wolfcamp A's and Wolfcamp B's in that area. And we ended up just beating IP records like I like Midland Basin IP records with these with these high pressure gas lift
33:38 setups. Wow. And so
33:41 when when I'm interacting with a customer, you know, I'm not just a compressor company coming in and being like, hey, here's a here's a package, take it and do what you want with it, right?
33:51 Like, I have enough context and have done this as a production engineer. Then I'm like, okay, they, they, they asked for my feedback and they're like, so what do we need to do to make this
34:02 successful? Like, and so I'm able to guide them through bottom hole design, through the wellhead design, flow lines all the way to the facility as a system to complement our high pressure gas lift
34:16 unit to make this, this project as, as successful as it that can be and maximize the results. That's really interesting when you have someone like you, it's an engineer, it's a subject matter
34:27 expert on a topic, solve this problem firsthand, develop solution for it, and now I'm being able to scale that to other oil and gas companies. And it's like, hey, it's not just a compression
34:39 company that you just will serve up a compressor based around a skid, like you actually have domain expertise and the problem that they're trying to solve. And so that's super interesting. When did
34:50 you start the companies? It's been a couple of years now Yeah, so we started in 2020 in the depths of COVID and negative oil prices. Yeah, cool.
35:02 Or relate to that, you know? It's an awesome time to be starting a company and a lot of
35:07 guests. Yeah, we built the first, so I met my partners through the paper I wrote. Yeah. I mean, honestly, had I not written that SP paper, this, we probably wouldn't be here right now.
35:18 Awesome, I'd love to hear that, you know, because I tell everyone, is the highest form of leverage of our generation and it doesn't matter if you're writing a blog post, if you're writing a white
35:26 paper, if you're recording a podcast,
35:29 good things come from creating content and so that's awesome to hear. Yeah, so I met my partners, we pulled some cash, built the first unit with our own money on spec with no customer and then
35:42 found a customer for it and you know that was by the time we got that unit out it was a spring 21 and then got that unit. Yeah, I mean, you know, get prototype built and field child. And then we
35:57 got our first big order with an anchor customer and then, you know, bagged a bunch of friends and family for some money and friends of friends and friends of family and check it's nice to call it
36:10 friends, families and fools. Yeah, exactly. And we were fortunate. We had a lot of, you know, a lot of our, and they're still all our equity partners. They're all, you know, we're.
36:21 entrepreneurs, OFS entrepreneurs themselves, and have successful businesses now, and really liked what we were doing,
36:31 and really took a chance on us, and there's something to be said for that as well, you know, digital walk-outers, all of our capital that we've raised has come from angel investors in the energy
36:44 industry, you know. It's good having champions on your side that, you know, they have networks, they have people that they can introduce you to, and then just inside on building successful
36:55 companies, so I'm sure you've all seen some element of that as well, going through that process. You know, talk a little bit about the, what I'm curious about is, you know, build this prototype
37:08 and you get it field tested, you know, year, year and a half sounds like a lot of companies out there struggle with the field tests and the pilot and, you know, MPs. way that they adopt
37:22 technology is they don't give a shit how cool it sounds, who else is using it. And so,
37:29 tell me a little bit about that. And you don't have to go into details about who the operator is or anything like that. But how are you able to convince someone to run this in a well? So by the
37:39 time we'd done this, there'd been a couple other compressor companies that started building a bunch of these same units off the back of, you know, the success we'd had previously at where I'd
37:50 worked before. And through the paper that I wrote, it was starting to gain some interest, and a lot of people were doing it. And so you have, you know, it all fields a small place, a bunch of
38:03 these engineers all know each other at different companies. So you're having beers, you're at some event or some, and you're talking with your buddies and one guy's like, Somebody's tried hybrid
38:13 gas lift, and somebody else hasn't, or they're talking about what they're doing at work and so
38:19 the it wasn't super radical by that point that it seemed like just something so far fetched that was hard to do, like enough people were doing it, that it wasn't too much of a hard sell. And a lot
38:34 of the work I have is just through relationships that I built over the years with other friends at oil companies that are other engineers, right? And so I think those relationships go really,
38:46 really far Yeah, I mean, that's one thing that's a constant. And every business is the soft skills and the network. I mean, you have a guy like you, super technical engineer, subject matter
38:59 expert on this operation. But ultimately, none of that matters if you don't have a way to go commercialize it and sell it, right? And so being able to rely on the network that you've built over
39:11 the years And I think also just kind of speaks to, you know, I love how you said that the market was actually kind of accepting of it because of the white paper you wrote and people are talking and
39:24 trying things like
39:27 this is something I think about a lot is sometimes you have to condition markets and condition industries and that white paper that you wrote was kind of setting that foundation for you fears down the
39:40 road because hey guys we've done this and that's success with this and you start getting other people thinking about it and now they're accepting of the idea and so
39:51 when you go to take your product to market you're not having to fight that battle of educating them and conditioning them for it. Another thing that made us super successful and I've done a couple
40:02 entrepreneurial ventures now in the OFS space is your partners that you go into these ventures with need to be really strong and you all need to have your experience. teas and complement each other
40:20 really well. So that like one plus one is 10, right? Not one plus one is two. Yeah, we need exponential math here. So I have to give a lot of credit to my partners because everybody within our
40:36 company is really strong operational and field backgrounds and has spent a lot of time, you know, providing services to oil companies or working at oil companies. So that's something that's
40:49 contributed a lot to our success is just knowing what we're talking about in the field. Yeah. And being able to execute in the field and not screw up too badly in the field, or if we do screw
40:58 something up, being like, okay, look, we messed up, we got this, we know what went wrong. This is the fix and we're fixing it right away. It's never gonna happen. Yeah. Yeah, you know,
41:10 picking the right partners can make a break. So it has to be an overwhelmingly Yes, this is the right
41:15 partner. Like I said, complimentary skill sets. Um, that way, you know, when you're building a company, man, it's fucking hard. And you have to cover a lot of ground. Everybody says that,
41:26 but you don't know until you've done it. Yeah. That's like, I even think sometimes I'm like, man, where would I be if I just like stayed at a cushy engineering job and just like got my salary and
41:38 my, my five weeks of PTO or whatever, my stock options, right? Like, like, but I think about, I'm like, I wouldn't trade that for anything. And like, I have the best time of my life I think
41:47 about this all the time because I'll be watching my friends Instagram stories and, you know, they're all investment bankers and they're done really well for themselves. And I was watching Instagram
41:58 stories. I'm like, God, am I an idiot? Like, why do I want to build companies? But it's the love of the game, right? And, you know, hopefully you have a good economic impact return for your
42:13 efforts But, you know, the, I never lied to talk like. There's a lot of people like, oh, you know, building businesses. It's hard. Like, that's not part of my rhetoric. I don't like talk
42:23 about that a lot, but it's funny. I was listening to two podcasts from Mark Zuckerberg this weekend. And even he was talking about, he's like, the businesses is, it's tough. And it's
42:33 challenging. And like, the thing is, is like, you never reach a point where it's not harder. Challenging is not like, oh, I've made it. Like, it's a business is a living organism and
42:43 continues to evolve And you have to iterate over time and so making sure that you have the right team in place to do that is super critical and just pick your heart. I mean, life's hard, man. So
42:56 yeah,
42:58 that's life is life is hard. So yeah, I mean, it's hard regardless. And so, you know, I've had a couple of friends recently, but overall, you know, throughout the years, I have a lot of
43:11 engineers that come to me and want to buy like, Hey, you know, should I go start a company? Should I join a start-up? You know, I had a real conversation with a friend the other day, you know,
43:20 he just had a kid and he's at Chevron and he's like, you know, here's my salary, here's my bonus, here's my pension, other benefits and as I say, dude, to be honest, it says it's not a bad
43:31 life. No, it's not a bad life. There's lots of people that have worked at majors and become multi millionaires just from doing that and really don't have to work that hard to make that happen.
43:41 It's like, it's not a bad life You really got to ask yourself, why? You're not going to go to a startup. It's not going to be easy. You got to put your weight. Who knows if you'll make any money
43:54 from it. Those are the types of things that you have to ask yourself. It's like, why am I doing this? It's from a pure economic standpoint. It's like the risk adjusted safe ways to go get a good
44:06 job. There's a lot of economic pain. Hopefully you get the payout at the end of it I've had a lot of economic pain. I'm hoping someday that I don't have that economic pain, but it's not today.
44:17 Man, this is super fascinating.
44:20 I hope, Juan, you gave a masterclass on artificial lift. I was setting you up for an alley youth there and took it to the rim in Duncan. So there's gonna be some awesome content coming out of that
44:30 on artificial lift 101. But for you, as we're signing off here, what's your ask? Are you looking for customers? Are you looking for investors? What's on the path for you guys?
44:41 We're just at a point where we're starting to scale, right? So, I felt like, I mean, we'd been talking for a couple of years about getting on the podcast. Yeah, honestly, yeah, a couple of
44:50 years on the make. And I felt like it was the right time now, we're at the right scale and I've established ourselves
44:59 well enough that I think it was the right time to do something like this and kind of broadcast us out
45:06 into the world. Oh man, this is exciting stuff, you know. I've,
45:12 fortunately, I think for me, I always get to see these things, you know, from, you know. the sidelines, and saw you in the early days, and you can tell people that I was always pushing you
45:23 like, Come on the podcast, come on the podcast, you know, like, not a tour heading.
45:28 I'm excited for you guys. I tried that here at that point, and before we end this podcast, this is your time to shine your pitch. Tell me why people should use Xtreme over any other competitors
45:39 out there Our thesis is threefold, more oil production for less operating costs and fewer emissions. So I mean by that. So more oil production using high pressure gas lift over ESPs or conventional
45:55 gas lift. Lower operating costs with our compressor package is called the Scout ULM. So lower operating costs with our Scout
46:06 ULM We've done so much engineering in house and manufacturing. Our package is honestly the best package out there. and our mechanical availability is the highest in the industry as well as we get
46:21 the highest throughput out of any competitor. So where one of our competitors would be at 18 million a day injection rate, where we're up to three million a day on our conventional two stage machine.
46:34 Ah, almost double. Yeah, almost double. And then third is our fewer, fewer missions. So we have a patented technology called our ultra low methane technology. We abbreviated it ULM. It's on
46:49 the back, our scout ULM. And what that ultra low methane technology does is four things. Number one, it eliminates fusion methane emissions by eliminating the use of process gas. So
47:06 we have electric starters, no use of process gas on starting up.
47:11 We've gotten rid of the use of process gas
47:15 So there's no process gas for pneumatic controls. The second part is where we can't eliminate it, we capture it. So we capture fugitive methane emissions off both the compressor frame and the
47:27 engine itself. So we capture those emissions and then feed it back into the intake to burn as fuel. And then
47:36 the third thing we do is
47:42 we
47:44 get rid of, so sustainable operating practices, right? So
47:49 usually when you, a unit goes down, you have to restart it. You have to blow down the unit to atmosphere. So we've gotten rid of that. You don't blow down the unit to atmosphere. You blow it
47:58 down through the blow case to where you dump like your liquids and stuff out of your scrubbers. And so you no longer have or blowing, you know, straight methane out into the atmosphere either.
48:10 It's pretty cool to hear about how y'all are capturing methane and dumping that back in. It is fuel as well, so it sounds like some pretty intricate engineering. And honestly, there are so many
48:21 companies out there that they're identifying methane leaks, whether it's on tanks or flares or using cameras. So many companies out there are identifying methane leaks, but how many companies are
48:33 actually doing something about the leaks? So what we're doing is we're identifying the points where you have these fusion methane emissions and we're capturing and eliminating them and we're
48:43 measuring them. And so when you get down to it, when you look at it from a CO2-E basis, scope one plus scope two. So what does that mean? Scope two emissions are like the emissions associated
48:55 with that specific thing. And then scope one emissions are upstream. So, no, there's the other way around. So scope one is that your thing that you're using. Yeah, it's your direct emissions.
49:06 Yeah, your direct emissions And scope two are the ones straight upstream. And so if you look in an electric package, like a lot of people are electrifying. compression right now because of
49:15 emissions. When you look at an electric package, you can't just ignore scope two emissions, right? You may not be having any direct combustion emissions on your package, but without the ULM
49:28 technology, and if you have an electric compressor, you still have fugitive methane emissions from all the other components, right? And then you have to take into consideration what the makeup of
49:39 that grid power is And when you look at both Scope 1 and Scope 2 emissions, our normal natural gas engine
49:49 3306 NA package is within 5 to 8 of
49:55 the Scope 1 and Scope 2 emissions CO2E as an electric package. Oh, wow. So
50:04 it's fascinating hearing about that because the engineering in itself is already tough in terms of. building a solution for a problem, an artificial lift, but then taking in the emissions factor as
50:17 well. I love how you said it. There's a ton of people out there that are monitoring emissions and identifying emissions, but actually creating solutions that capture them and solve them. And so
50:27 super interesting to hear about how you guys think about that. And then you get back to like, we talked about electrical infrastructure earlier with ESPs. Like one great thing about gas-fired
50:38 natural gas compressors is you don't need electricity And so if you start setting all your compressors now or electric, you're dealing with the same electrical issues as you do with
50:49 ESPs of power quality and power distribution and building out the grid and things like that. And we are building a certain percentage of our fleet, electric. But in these remote locations, it's
51:01 just not feasible. You can't put all electric compression out there. So you have to have a good, clean combustion option That is also. you know,
51:15 environmentally sustainable. Yeah, so, engineers that are listening to this, where can they find extreme on the internet? If they're interested in y'all's
51:26 solution. Find you on LinkedIn, find you online. Yeah, find me, Brandon Prank on LinkedIn, find extreme lift on LinkedIn. It's spelled, we spell a little bit weird. It's X, S-T-R-E-A-M lift,
51:40 or extreme liftcom. If you're watching video, here's a sticker at extreme lift, we'll drop a link into the show notes, check it out, find Brandon on
51:51 LinkedIn, hopefully someday soon collide. if y'all aren't over on Collide. Brendan, thanks for coming on, man. Thanks, Colin, appreciate it.
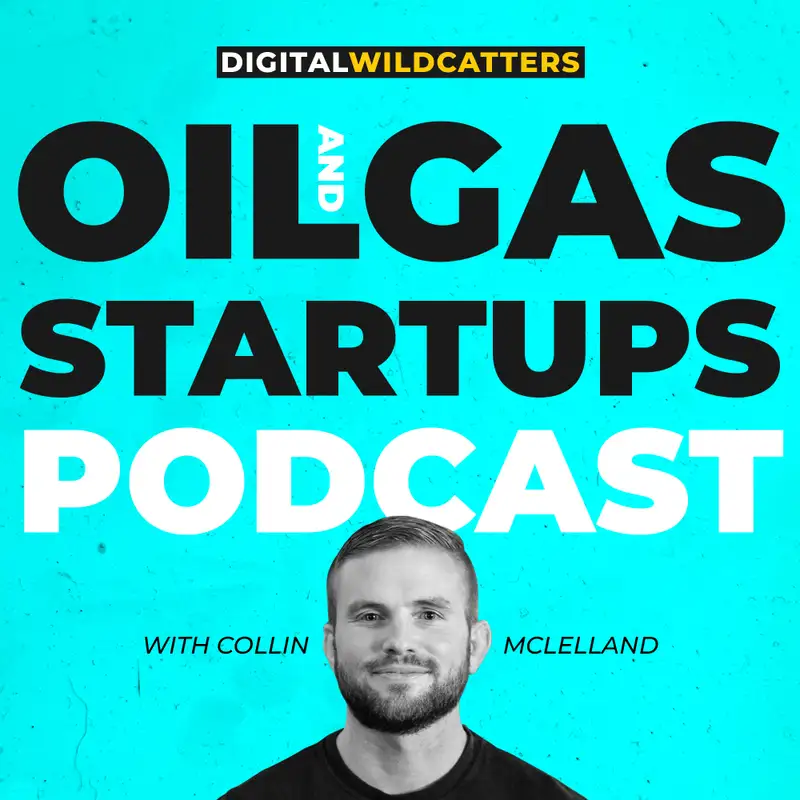